PRODUCTS
MIXING SYSTEM
Ensuring stability and uniformity by homogeneously mixing various materials.
Various impeller and jacket designs are applied for effective dispersion and mixing of materials, greatly enhancing production process efficiency and mixture quality.
- SUPER MIXER & COMBI MIXER & LAB MIXER
- COOLING MIXER (BLENDER)
- ADDITIVE MIXER
- FLOATING MIXER
- COLORING MIXER
- HIGH SPEED MIXER
SUPER MIXER & COMBI MIXER & LAB MIXER
Used as key equipment in compounding processes due to high-speed mixing and high homogeneity, providing efficient mixing performance under various material and process conditions.
Excellent blending efficiency with rotating upper/lower impellers and deflectors.
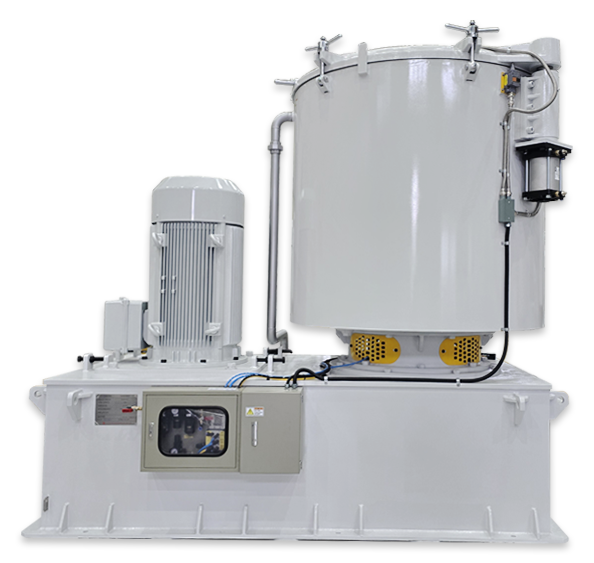
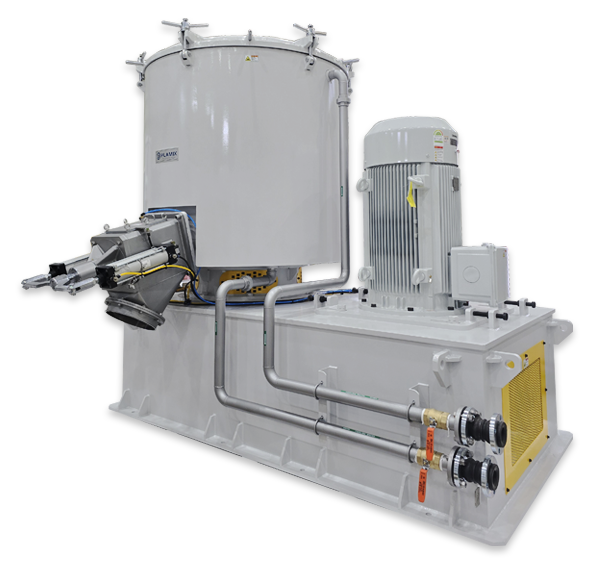
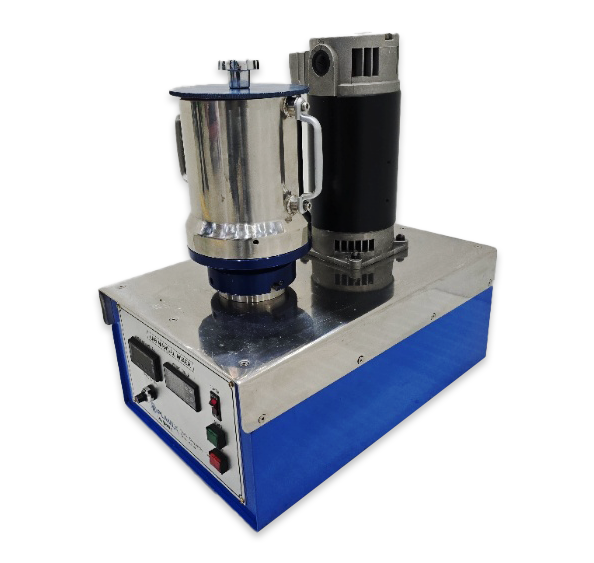
PURPOSE
1. High-Speed Mixing
Forming uniform mixtures by rapidly mixing polymers, additives, fillers, etc., at high speed in a short time.
2. Ensuring Homogeneity
Improving product quality and realizing material properties (strength, durability, etc.) through uniform dispersion of materials.
3. Process Efficiency
Saving production time and energy with rapid mixing, ensuring efficiency in mass production.
FEATURE
1. Safe and Uniform Mixing
Maintaining product consistency through rapid and uniform mixing via high-speed rotation and even dispersion of additives.
2. Application of Various Impellers
Customizable mixing tailored to material characteristics.
3. Fully Enclosed Structure
Maintaining a clean process by preventing dust scattering and foreign substance intrusion.
4. Scalability of Application Range
Applicable to various materials such as secondary batteries, polymers, and additives.
APPLICATION
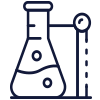
CHEMICAL
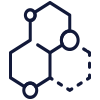
POLYMER
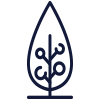
RECYCLING
TECHNICAL DATA SHEET
se | Model | Total Capa | Working Capa | Impeller R.P.M | Motor | Dimension | ||
A | B | C | ||||||
Blending | JMX-50S | 50L | 33L | 680 RPM | 3.7kW | 650 | 1630 | 1312 |
JMX-100S | 100L | 66L | 630 RPM | 5.5kW | 670 | 2110 | 1475 | |
JMX-200S | 200L | 132L | 600 RPM | 11kW | 850 | 2365 | 1535 | |
JMX-300S | 300L | 200L | 580 RPM | 22kW | 860 | 2750 | 1650 | |
JMX-500S | 500L | 330L | 450 RPM | 37kW | 960 | 2840 | 2085 | |
JMX-750S | 750L | 500L | 400 RPM | 55kW | 1160 | 3120 | 2220 | |
JMX-1000S | 1000L | 660L | 375 RPM | 75kW | 1220 | 3380 | 2240 | |
JMX-1500S | 1500L | 1000L | 330 RPM | 150kW | 1300 | 3420 | 2390 | |
Heating | JMX-500HS | 500L | 330L | 600 RPM | 75kW | 960 | 2840 | 2085 |
JMX-750HS | 750L | 500L | 550 RPM | 120kW | 1160 | 3120 | 2220 | |
JMX-1000HS | 1000L | 660L | 480 RPM | 150kW | 1220 | 3380 | 2240 | |
JMX-1500HS | 1500L | 1000L | 330 RPM | 190kW | 1300 | 3420 | 2390 |
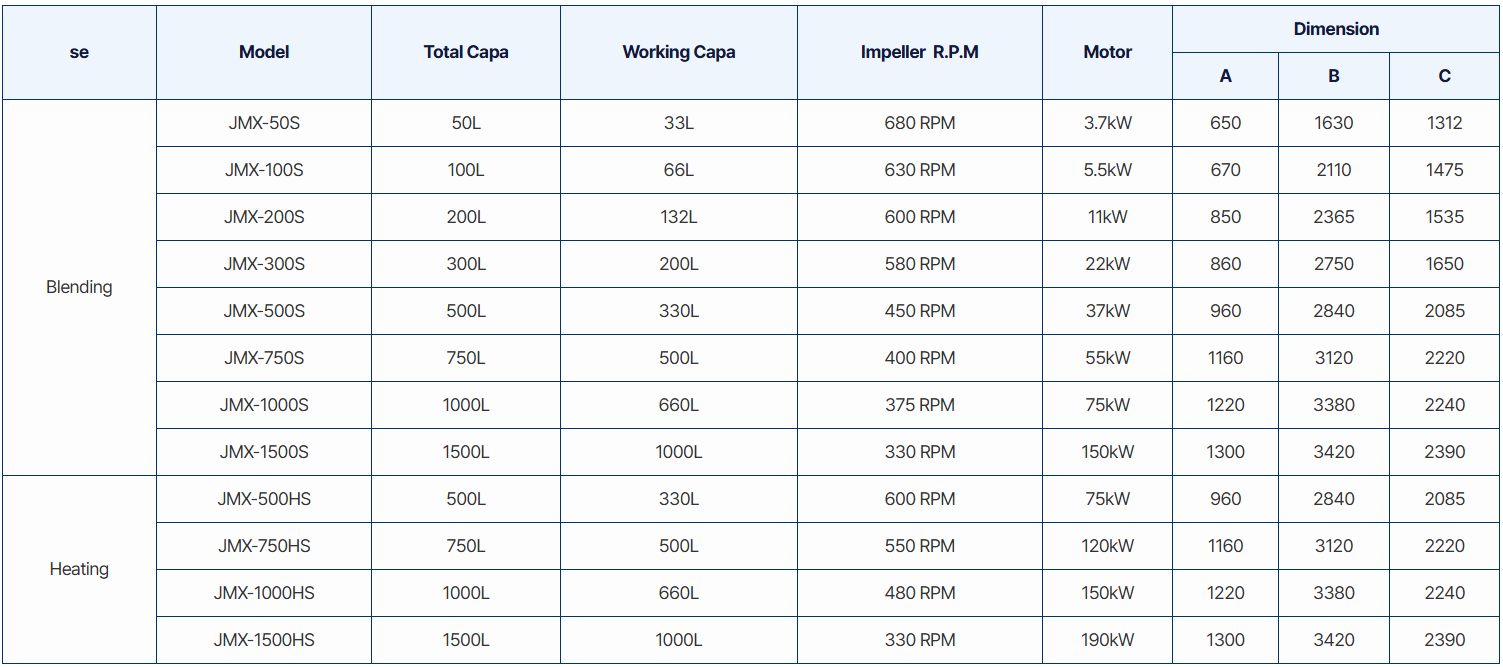
※ Please contact us for LAB MIXER technical specifications.
DIMENSION
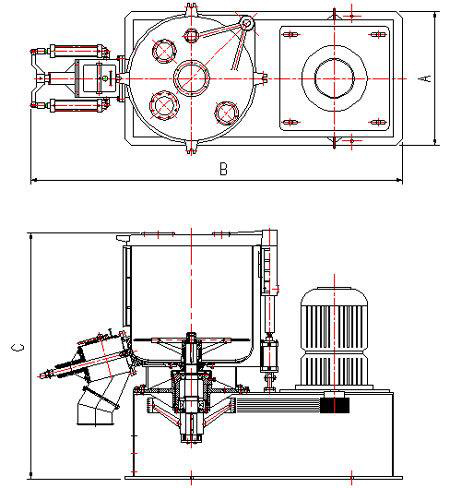
COOLING MIXER (BLENDER)
Maintaining the quality and characteristics of PVC products through rapid cooling after high-temperature mixing.
Maximizing productivity with a design that enhances cooling efficiency and maintenance convenience.
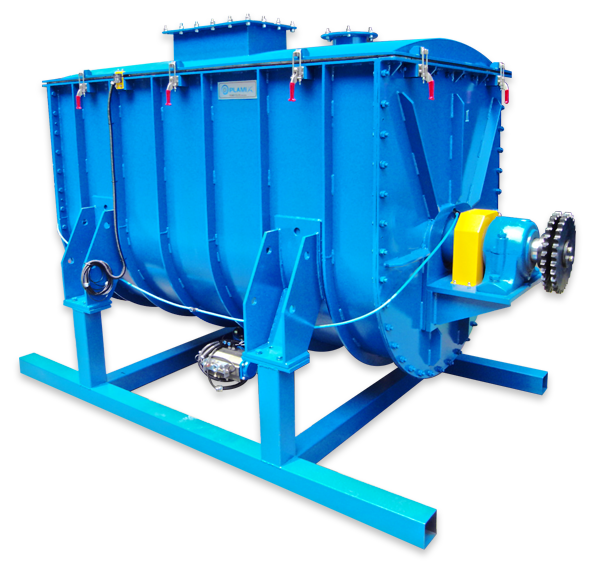
PURPOSE
1. Cooling and Stabilization
Maintaining product quality and characteristics through rapid cooling of high-temperature mixtures.
2. Product Quality Improvement
Preventing thermal deformation and providing uniform temperature distribution.
FEATURE
1. Spiral Cooling Jacket
Implementing fast and efficient cooling through a wide heat exchange surface area.
2. Easy-to-Replace Impeller
Reducing maintenance costs and time with easy replacement in case of wear.
3. Durability and Stability
Ensuring reliability with the use of high-durability materials.
4. Uniform Cooling
Contributing to defect-free product manufacturing by ensuring thermal stability.
APPLICATION
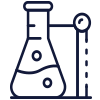
CHEMICAL
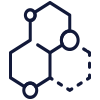
POLYMER
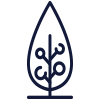
RECYCLING
TECHNICAL DATA SHEET
Model | Total Capa | WorkingCapa | Impeller R.P.M | Motor | Dimension | ||
A | B | C | |||||
JMX-1000C | 1000L | 300L | 35 RPM | 5.5kW | 1720 | 2680 | 1300 |
JMX-1500C | 1500L | 500L | 35 RPM | 11kW | 1900 | 3010 | 1450 |
JMX-2100C | 2100L | 700L | 30 RPM | 15kW | 2050 | 3250 | 1550 |
JMX-3000C | 3000L | 1000L | 25 RPM | 19~22kW | 2300 | 3700 | 1750 |

DIMENSION
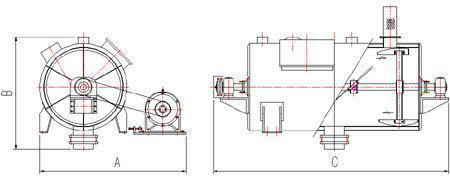
ADDITIVE MIXER
Producing high-quality products through high-efficiency mixing and uniform dispersion of additives.
Playing an important role in various industries with excellent cooling efficiency and maintenance convenience.
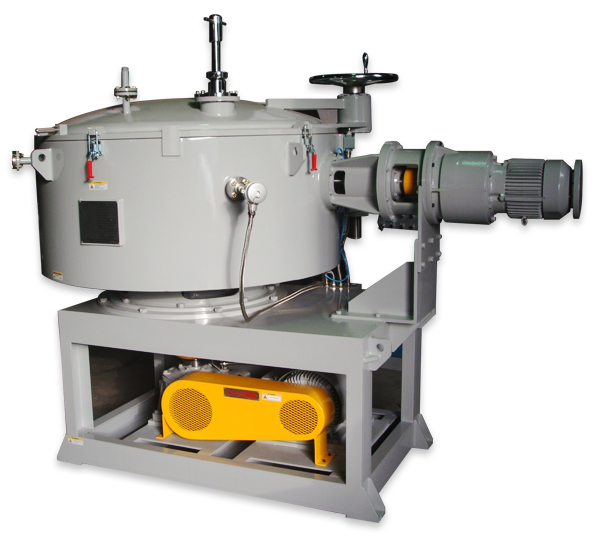
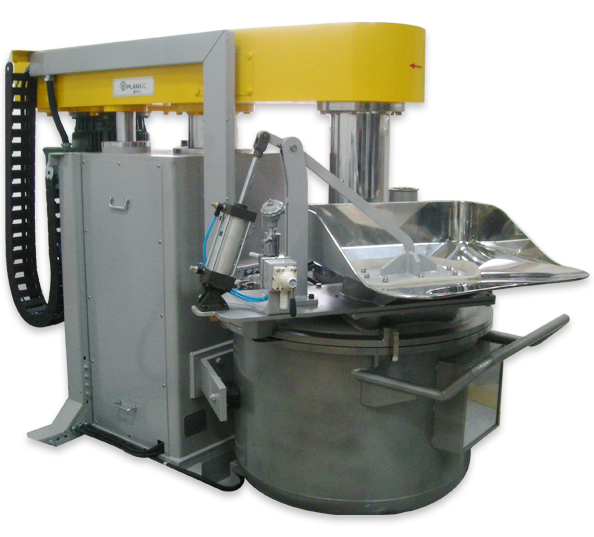
PURPOSE
1. Uniform Additive Mixing
Realizing desired material properties (strength, durability, color, etc.).
2. Maximizing Mixing Efficiency
Achieving uniform dispersion with a combination of impeller and deflector.
3. Cooling and Quality Maintenance
Maintaining product quality through heat dissipation via a jacket.
FEATURE
1. Dual Impeller System
Achieving fine grinding and dispersion simultaneously with raw material mixing.
2. Ease of Cleaning
Easy-to-clean internal structure prevents contamination and facilitates maintenance.
3. Expanding Additive Application Range
Enabling uniform dispersion of various additives.
APPLICATION
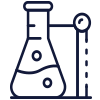
CHEMICAL
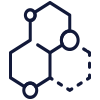
POLYMER
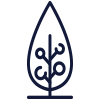
RECYCLING
FLOATING MIXER
Equipment optimized for small-batch material compounding, enhancing work efficiency and ease of cleaning.
Improving blending efficiency and enabling mixing of various additives through high-speed vibration function.
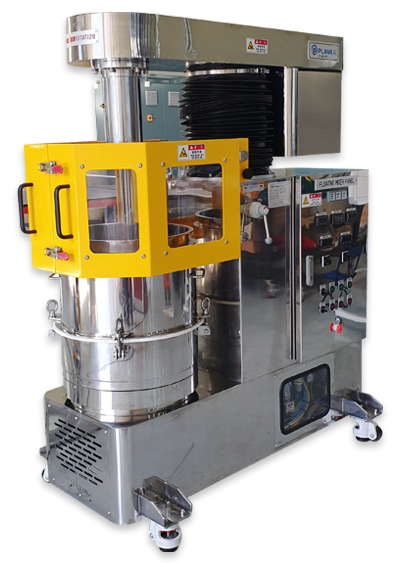
PURPOSE
1. Small-Quantity Additive Compounding
Maintaining quality through uniform mixing of precise materials.
2. Maximizing Work Efficiency
Providing simplified input/output processes and an easy-to-clean structure.
FEATURE
1. Suitable for Small-Quantity Colorant Compounding
Optimized for high-precision color realization and use of special additives.
2. Pneumatic Lifting and Lowering
Easy internal cleaning and maintenance after mixing.
3. Vinyl Bag Input and Discharge
Preventing foreign substance contamination and supporting quick work transitions.
4. Impeller Rotation and High-Speed Vibration
Reducing material loss and improving mixture homogeneity.
APPLICATION
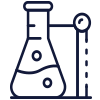
CHEMICAL
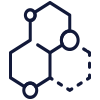
POLYMER
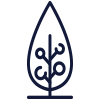
RECYCLING
COLORING MIXER
Uniformly mixing colorants into raw materials to maintain color consistency and quality.
Playing an important role through high productivity and mixing efficiency.
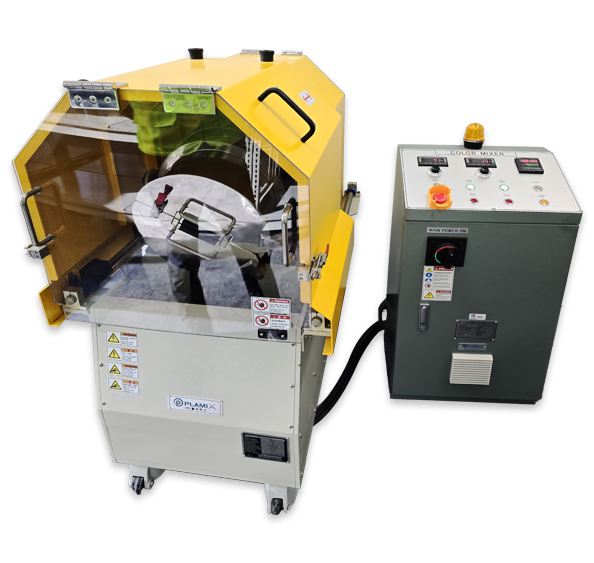
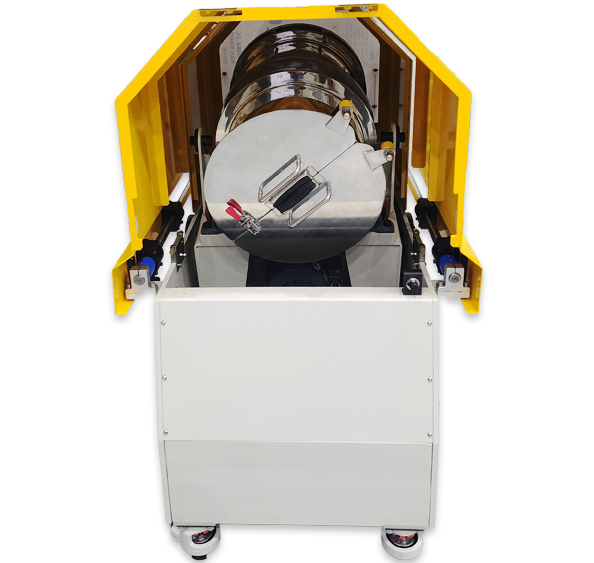
PURPOSE
1. Efficient Compounding of Small-Quantity Colorants
Aiming for Precise Color Realization
2. Worker Safety Protection
Preventing musculoskeletal disorders and increasing convenience.
3. Maximizing Cleaning and Work Efficiency
No cleaning required during color changes.
FEATURE
1. Suitable for Small-Quantity Colorant Mixing
Enabling fast and accurate compounding of various colors.
2. Easy Input Method
Enabling transition without production stoppage during color changes using a vinyl bag input method.
3. Drum Rotation and Swing Motion
Ensuring mixing efficiency and uniform color quality.
4. Worker Protection Design
Ensuring safety and convenience with an ergonomic design.
APPLICATION
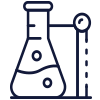
CHEMICAL
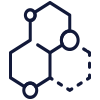
POLYMER
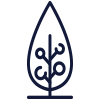
RECYCLING
HIGH SPEED MIXER
Supporting product quality improvement and process efficiency through electrode slurry mixing in secondary battery processes.
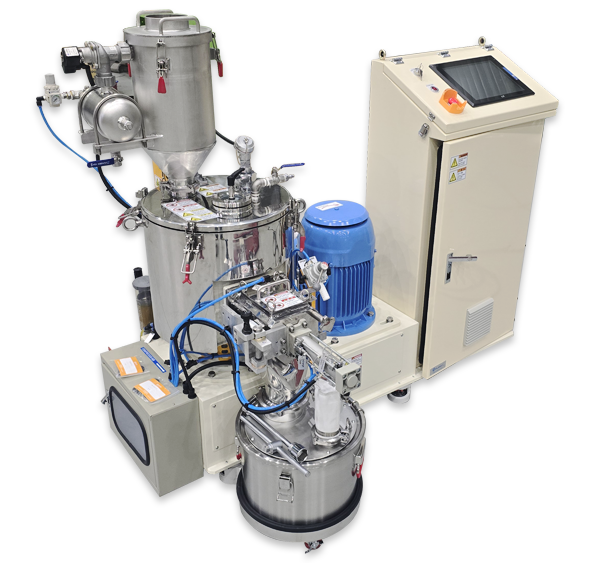
PURPOSE
1. Electrode Slurry Mixing
Uniform mixing for optimizing electrical performance.
2. Efficient Production Process
Improving production speed and saving energy through rapid mixing.
3. Consistent Product Quality
Improving battery performance and lifespan by controlling viscosity and homogeneity.
FEATURE
1. High-Speed Mixing
Ensuring slurry homogeneity through powerful rotational force.
2. Optimized Design
Application of special materials to prevent metallic foreign substance contamination.
3. Fully Enclosed Structure
Minimizing dust and maintaining a clean working environment.
4. Temperature and Viscosity Control
Managing heat generated during mixing and maintaining consistent viscosity.
5. Automation and Ease of Operation
Simplified condition setting and monitoring through a control system.
APPLICATION
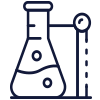
SECONDARY BATTERY
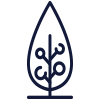
RECYCLING
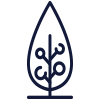